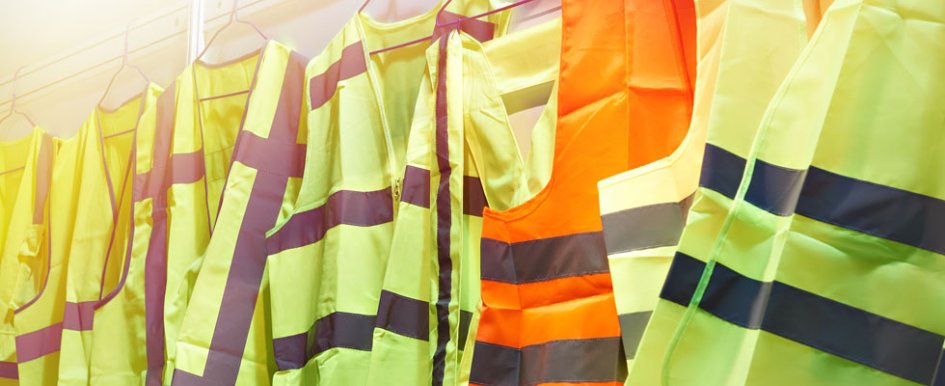
Supply-chain delays caused by COVID-19 are often an inconvenience, but can also be an employee safety issue. Global supply-chain disruptions in shipments of American National Standards Institute (ANSI) high-visibility safety apparel create a safety risk for construction workers who rely on the effectiveness of reflective garments to be visible in hazardous conditions. Goods shipped via container ships to the United States from China, where many reflective materials are manufactured, used to take approximately 40 days to arrive, but now often take upward of 70 days.
Companies not prepared for such delays may experience gaps in critical safety equipment.
While some safety equipment, such as hard hats, have an expiration date of up to four years, other safety gear, such as high-visibility apparel, must be replaced more frequently to ensure employee safety. On average, high-visibility garments last up to six months, but often need to be replaced sooner, depending upon the use and care of the garment.
While proper care prolongs the life of safety apparel, reflective and fluorescent materials lose effectiveness over time. A garment that might appear fine to an employee may in fact not be reflecting properly. Unfortunately, many employees are not adequately trained to inspect reflective apparel. This may cause decreased visibility, particularly in poor weather conditions. Without the proper safety gear, employees are at a greater risk of injuries.
How often high-visibility gear should be replaced depends upon several factors, including how often the garment has been worn, how often it has been washed, how it has been cared for, and the extremity of working conditions. For instance, garments worn in rain and snow lose their effectiveness sooner than garments worn infrequently indoors.
Simon Heaney, senior manager of container research at maritime research firm Drewry, predicts that supply will lag behind demand in the container market throughout 2022, but he anticipates that the “frenzy of orders for new containerships” will lead to a risk of overcapacity returning to the market in 2023 and beyond.
A recently published study from consulting firm Deloitte, “2022 Engineering and Construction Industry Outlook,” shared that: “Overall, supply-chain disruptions and volatility are expected to be among the biggest challenges in 2022, and the firms that can navigate through them will likely emerge as winners.”
So, what can construction business owners do to stay ahead of safety gear supply-chain delays? Consider the following five strategies to help mitigate the impact of high-visibility apparel supply-chain delays to ensure employees have proper safety attire.
1. Conduct an Inventory Assessment
Conduct a full inventory of the high-visibility safety apparel you have on hand and the supplies you might be running low on. Then review your outlook for 2022.
Assess not only your immediate needs, but also consider what your needs will be throughout the year. Is your firm expecting an increase or decrease in demand? Has your firm landed large new contracts that will require a large increase in safety equipment? Is your firm anticipating an increase in projects because of the Infrastructure Investment and Jobs Act? Is your firm venturing into a new sector that will result in significant growth? In addition, examine past purchase-order lead times so you have a baseline for adjusting replacement timelines.
2. Evaluate Shipping Delays
Next, contact your vendor and ask how supply-chain delays are impacting their services, if at all. Ask for estimates of delivery timelines on specific products you expect to order. Find out which products your supplier has in stock and which products are delayed. Examine current needs versus product availability. If there is a significant delay in a desired product, ask your vendor for recommendations of alternative products. The key is to be flexible.
While some products may be unavailable or have extended timelines, many high-visibility products are in stock.
3. Maintain Safety Standards
Even though adjustments may be made to the type or style of reflective apparel worn, it is critical to adhere to safety standards, such as the American National Standard for High-Visibility Safety Apparel and Accessories (ANSI/ISEA 107-2015) standard. High-visibility safety apparel is classified as Class 1, Class 2 or Class 3, based on the amount of reflective material and the level of contrast (orange or lime color) of the fabric.
Class 1 safety garments are for low-impact work environments. Class 2 attire is for employees working near traffic or in low-visibility areas. Class 3 garments are for employees working in high-traffic areas or hazardous situations, such as near heavy equipment. No compromises should be made that violate guidelines.
4. Create Succession Plans
Evaluate replacement timelines and adjust for possible shipping delays. Adjust your purchase schedule by purchasing supplies with the longest lead times first. Build in additional time for large quantities of gear or custom orders, such as high-visibility jackets with custom logos. Establish a succession plan to replace gear before it becomes a safety. Structured safety programs that function on a set schedule help to remove inconsistencies related to human factors, such as independent apparel maintenance and inspection. Structured programs are also budget-friendly and allow for more accurate forecasting and business planning.
5. Prolong the Life of Existing Gear & Apparel
Reflective garments that are not properly cared for lose their effectiveness early and unnecessarily increase the demand for replacement garments.
Since employees should never use reflective garments that have lost their effectiveness, all dull, faded, scratched or torn garments should be replaced immediately. Employees should also replace garments after the recommended number of washings.
Employees can maximize the life of reflective garments through proper care such as not washing reflective apparel with materials that have a rough finish, such as jeans, turning garments inside out before washing, avoiding fabric softeners, which may damage reflective tape and drying reflective apparel on a line instead of putting it in the dryer, as the heat will damage reflective tape. Additionally, make sure not to wash reflective garments with dark garments, as that exposure may reduce the intensity of fluorescent materials, removing dirt and storing reflective garments away from direct sunlight and without crushing reflective tape. With proper planning, your construction business can keep its employees safe by staying ahead of supply-chain delays that impact shipments of safety gear.