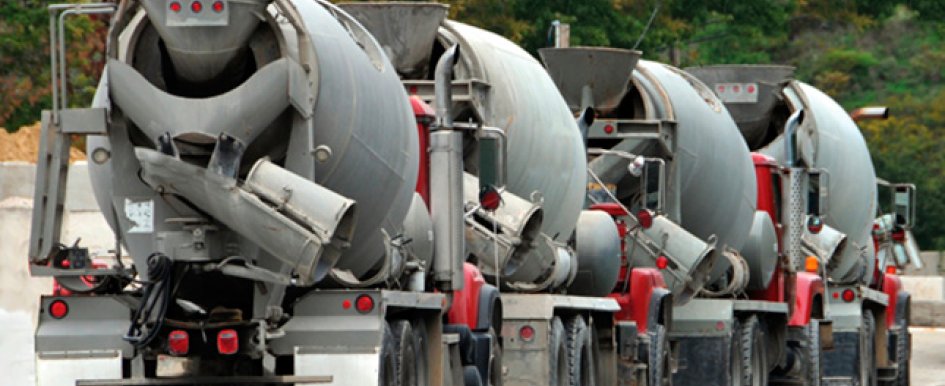
The heavy construction market segment is a vibrant industry comprised of companies that provide a broad array of engineering, consulting, construction, management, planning and design services for a wide variety of infrastructure projects servicing many types of clients. With a market share of about 10 percent and a value of more than $701 billion for nonresidential construction, the United States is the second-largest construction market worldwide.
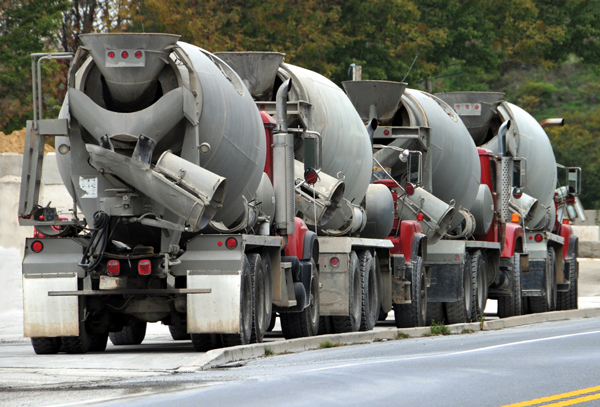
Encompassing a diverse range of projects from highways, bridges and mass-transit systems to commercial buildings, oil and gas exploration sites and wastewater infrastructure, one common thread among all of these is the dynamic operation, use and servicing of essential heavy-duty vehicles and equipment.
Predicting the potential client's spending potential is just that—a prediction, based as much on cyclical economic patterns as it is on statistical analysis. However, some spending does follow predictable trends. For instance, many commercial clients will increase investment during the middle and late stages of an economic expansion. They usually cut spending in downturns, and the opposite holds true for municipalities.
With all of these variables, one thing remains a constant for every construction operation, regardless of the client, project size or fleet size—fuel consumption.
A construction fleet can consume hundreds of gallons of diesel fuel per day. Based on an average engine load for some of the most common pieces of equipment, which can consume an average of three to six gallons of diesel fuel an hour, fuel management becomes one of the biggest daily expenses for any project.
When it comes to managing fuel consumption on a construction site, at the end of the day, the week or the month, profit comes down to the difference between the fuel you pumped and the fuel you bought. Typically, fleets would not want to see a difference that exceeds 2 percent. At a difference of 2 percent, that's a lot of spilled fuel. But is it spilled? Missing fuel can be unaccounted for due to misappropriation to another site or from outright theft. In these cases, accountability becomes a matter of profit and loss.
Managing the level of available fuel within the holding tank is another key task critical to keeping the equipment operating. If the operation slows or stops due to a lack of fuel, the bottom line is impacted immediately.
The Challenge
A main priority for construction operators utilizing a fueling station should be to know just how much fuel is inside any of the site's storage tanks at any moment. Sticking tanks to gauge fuel levels may still be popular with many companies, but the accuracy of this process is questionable. Computer-aided tank-gauging technology is now available to measure and record product level to the tenth of an inch.
Another challenge for many construction companies is identifying exactly who is responsible for monitoring and recording inventory levels. No matter the size of the company, there is often a lack of coordination and communication between various arms of the organization. This can result in additional reporting processes that can lead to a drain on company resources and the potential for greater risk and liability.
The proper knowledge and experience in managing fueling operations is becoming more and more important as critical compliance regulations grow more rigid each year. Federal, state and local authorities are becoming more vigilant and their regulations increasingly more complex with regard to release detection and reporting, spill prevention, corrosion protection, air quality, atmospheric releases of volatile organic compounds (VOC) and the presence of hazardous substances at a fueling site.
Service costs can also be a drain on a construction operation that does not have the most advanced fuel management program in place. Many sites rely on a local service provider when any fuel maintenance or alarm issues arise.
This can lead to increased costs, especially if the call is made during off-hours or if the problem occurs at an out-of-the-way location. A speculative "something's not working" call most likely will lead to two service trips: the first for the technician to assess the problem and the second to return with the parts or equipment needed to fix it.
Another challenge is creating the ability to keep accurate records of when repairs were performed and the subsequent cost. Not proactively identifying recurring maintenance issues can result in increased costs brought on by needless service calls.
The construction company that has not adopted centralized data management for its project operations, or whose managers have not automated their fuel management processes, is likely running a system that may be working on the surface, but not working efficiently. The benefits of automated fuel management for construction operations are numerous.
Automated Fuel Tracking
Automated fuel tracking allows real-time access to inventory levels and fueling habits at any time of the day or night for all of a company's fueling operations. It provides a more accurate account of both the amount of fuel usage at a facility and exactly where that fuel is going, which will decrease opportunities for theft. From a corporate standpoint, all fueling activities may be monitored from a central, regional or national office.
Reduced Maintenance Costs
Maintenance issues cause headaches not only when a piece of equipment fails, but also when the issue needs to be documented. If this data is not accurately recorded, the site operator runs the risk of overpaying for or repeating service calls. Fuel management services can let the operator know how much time the technician spent on-site, which is something that can be hard to track manually.
Compliance Management
Automated fuel management systems have been designed to track and update compliance data and incidents 24/7/365. Compliance management at commercial or industrial sites can be a lower priority, but automated management of this process increases its importance in the system without increasing the amount of employee interactions.
Alarm Management
Alarm management is traditionally a labor-intensive, manual job. With the implementation of automated fuel management, this difficult task can be outsourced to a company that can accurately diagnose, solve and document alarm conditions immediately.
Detecting an alarm event at the earliest possible point is essential to identifying a potential environmental risk and mitigating the costs that can be associated with environmental remediation.
Manage Contractor Database
Unless a site operator has a long-standing relationship with a service professional, they enter the unknown when on-site repairs or maintenance are needed. Automated fuel management systems allow a contractor database to be set up for the site, often by the company that is providing the fuel management service. This ensures that contractors who don't have the ability—or even current or correct insurance—are not called for a particular job.
Fuel is the essential cost of any business with fleets of vehicles. Having inaccurate inventory levels, even when technology is available for accurate inventory measurement, is simply unnecessary and a risk to a construction outfit's bottom line.
Automated Fuel Management
As today's fuel and transportation costs continue to be volatile, implementing an automated fuel management system into an operation is one way to immediately impact an operation's accountability and profit.
The modern automated fuel management system can easily provide fueling-facility managers, owners, fuel buyers and fuel suppliers with an end-to-end fuel management solution. Centralizing the capture and storage of key fueling-site information through automated processes ensures the end-user creates and maintains consistent site operations, delivering maximized operational efficiencies and site profitability.
Proven professionals in the compliance, alarm, service and project-management segments can provide best management practices (BMPs) for everyday operations. The BMPs for fuel management will improve operating efficiencies, reduce costs and minimize environmental impact. An account manager possessing expertise in fuel handling and fuel systems is involved in managing all options for any reputable service. In addition to savings, the reduction of the carbon footprint is often a residual benefit of the new fuel management tactic.